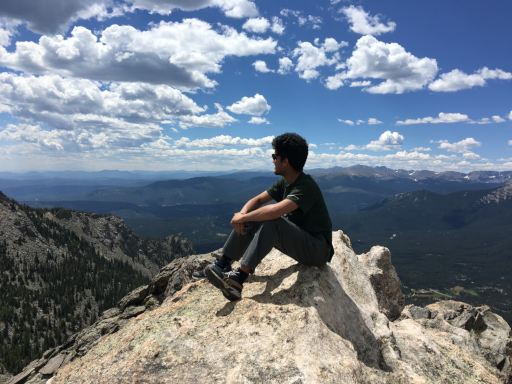
Guru Mulay
>> M.S. in Computer Science at CSU Computer Vision Lab
>> Interested in Machine Learning, Computer Vision, Robotics, Embedded Electronics, and many more...
>> guru5[-aT-]colostate.edu
You May Also Enjoy
HCI principle: Gulf of Evaluation in wild
1 minute read
Published:
A short intro to EGGNOG dataset
less than 1 minute read
Published:
Once I dissected a MAXON motor (well, not entirely but only encoder part, but even that was not recommended!)
5 minute read
Published:
Premise: Robotics team that I am a part of uses lots of different types of DC, BLDC, servo, and stepper motors. For example, we use wiper motors for high torque applications, DC Maxon motors for fault tolerant applications that need both high speeds (high RPM) and high torques. We also use low-end, economic motors (I do not know their names but they look like this) for prototyping purpose and places on Robots where efficiency and accuracy is not critical, for instance, for a extendable arm. Sometimes, we use BLDC for the applications where speed is critical such as propelling a robot. Stepper motors are used to get finer control over the motion derived from the motor's rotation. Servos are must where extreme torques are required. For example, a robotic jaw that grabs on to objects for significantly longer amounts of time. Servo motors gives a great control over precise angular motions.
How I got an expensive sensor for free from a major sensor company
3 minute read
Published: